PRECISION ON DISPLAY IN STATOR PROJECT
A project to remove and replace a 1,073,000 pound stator was recently featured in the May issue of American Cranes and Transport. What made this project notable was the precise calculations and testing that went into making the project a success.
The project was scheduled during an outage at a nuclear power plant in New Jersey. But before anything could be done, load tests had to be performed, including one at Barnhart’s Memphis location.
The Memphis team assembled a Modular Lift Tower (MLT) frame in their branch yard. The test load weight, including support girders, was 1,332,160 pounds or 125% of the lift load. Once the test was completed, Barnhart match marked more than 600 components and transported them to the New Jersey site.
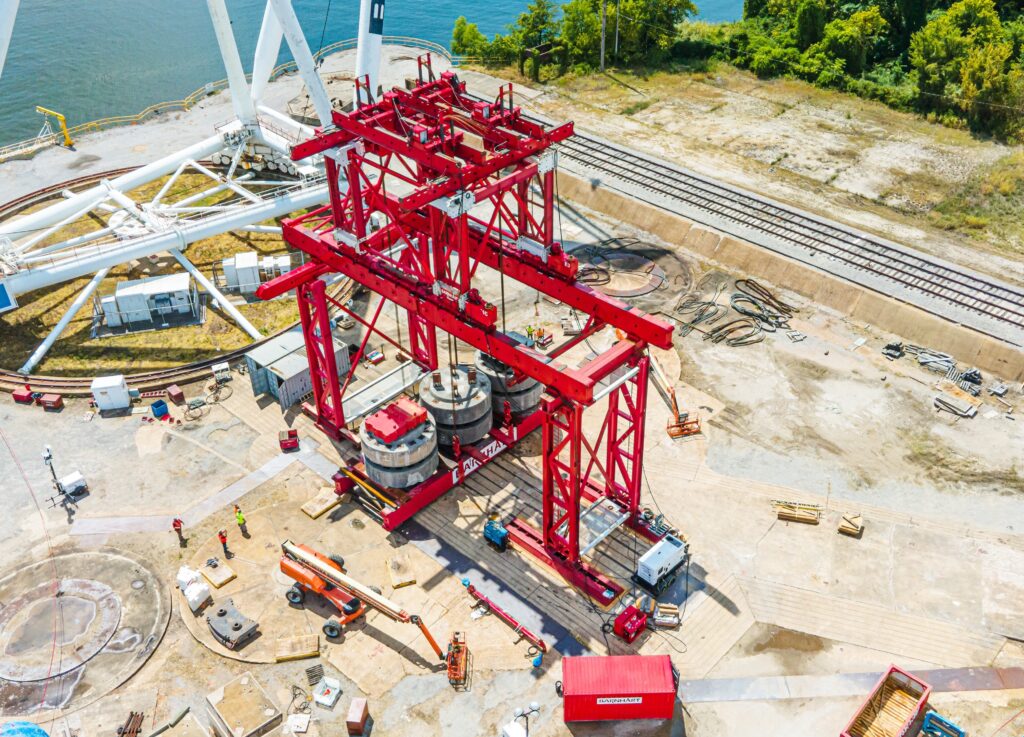
At the site, the stator was located on a 47-foot, 7-inch tall pedestal on top of a building. Its replacement was staged outside near the plant dock. Hydraulic gantries would be used to load and unload the new stator.
Barnhart had to match mark and reassemble the testing components. The MLT and a 750-ton hydraulic turntable and slide system were utilized to rotate the stator beneath the lift tower. A hydraulic transporter was used for onsite transport of the existing and replacement stator.
There was very little room to work in. The Lift Tower was tight between two water tanks, overhead gantry crane bents and a turbine building. There was just one foot of clearance between the turbine building and stator during the lift tower operations. An adjustable rigging link system was used to lower the stator.
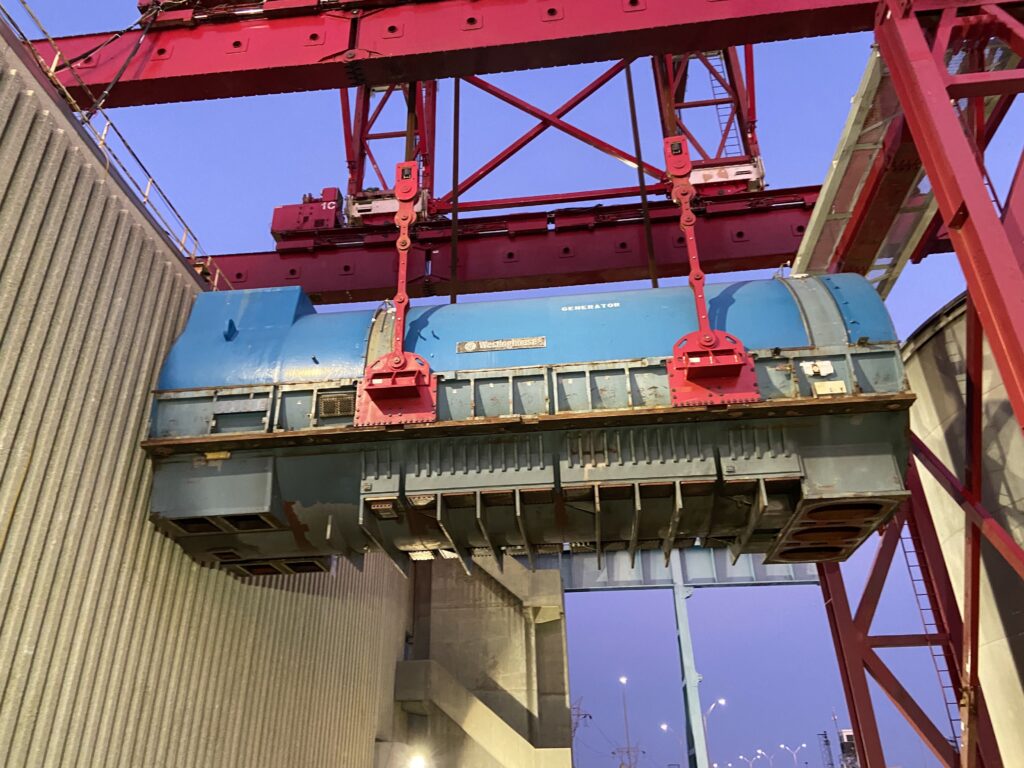
Other complicating factors included underground utilities which required shoring as well as matting of the area. Plus a tropical storm that hit during tower erection, which caused erosion.
According to the customer, the project required more than 50 calculation packages and 70 drawings. But they paid off in a project that was completed safely and without incident.