Wind Project Uses Innovative Method
A recent project at a wind farm in West Texas employed a revolutionary method for blade and bearing replacement in the wind industry. Barnhart used a new “craneless” method to complete the project.
Customarily, a replacement project requires two and sometimes three cranes. By eliminating even one crane in the process, the cost of mobilizing that crane, along with its crew, are also eliminated.
However, craneless does not mean completely crane-free. Instead this system utilizes smaller assist crane and ancillary equipment in place of the large crawler cranes that are normally used to exchange blades and bearings.
Barnhart, in partnership with Windcare India, introduced this method of blade and bearing exchange for the first time in North America. For the first time ever in the world, it was also utilized on this particular turbine platform.
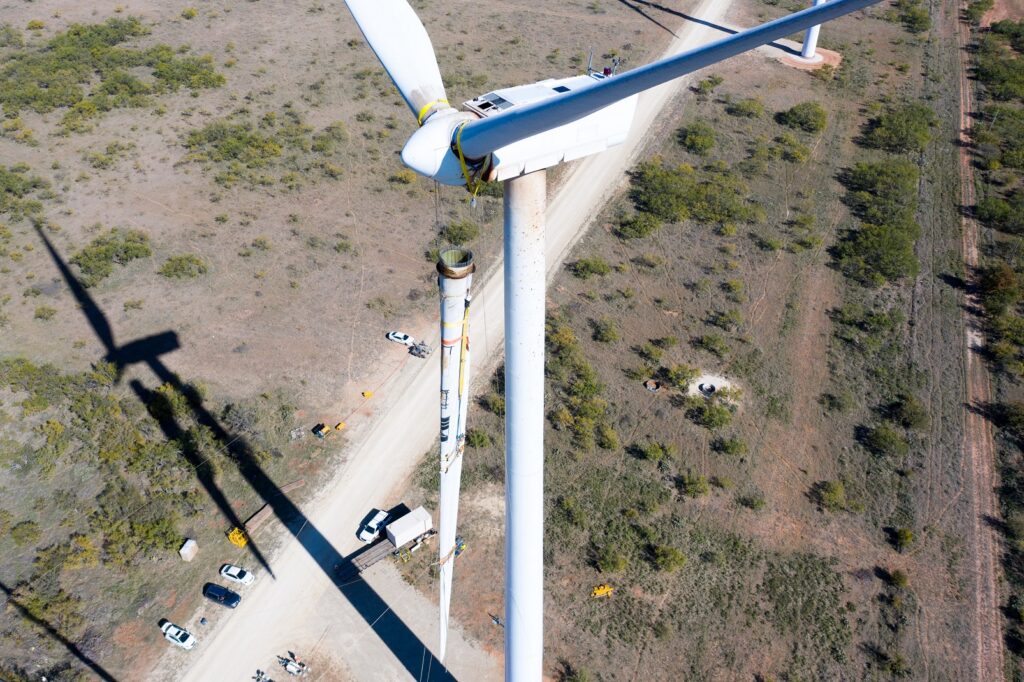
Rotor Lock Plates and Blade Tacos
There were multiple challenging steps during this execution of this project. For instance, the rotor for this specific tower would not lock at the 6 o’clock position, which was essential to execute the craneless method. The engineering team quickly designed and fabricated a rotor lock plate on site to address this issue.
The first successful blade bearing exchange was completed last summer in Abilene. Following that, the system was tested on a blade from a different manufacturer. Due to this blade’s structural integrity, which was different from the previous one, the blade was damaged during the exchange.
In response, the Barnhart technical team worked together quickly and developed a modified procedure to utilize trailing edge and leading edge protection (or blade tacos). Once the new rigging method was approved by the customer and their technical team, Barnhart mobilized on site.
The field team completed the project safely in two phases. The first phase lowered the damaged blade using the craneless system, with the modified trailing edge and leading edge protection. The second step safely raised the blade using the same system after the repair was completed by a third-party. Barnhart used two different teams on the project, which required over 4000 total man-hours.
The job was completed safely and efficiently and resulted in a client that was happy to see the turbine up and running again.