Barnhart Tackles Challenging Projects with Award-Winning Results
Faced with the threat of a collapsing scrubber unit, a power plant in New Jersey made an emergency call to Barnhart. A thousand miles away, another branch wrestled with how to remove and replace 12 reactor legs at a chemical plant in Florida.
Barnhart’s innovative solutions to both projects resulted in two recent SC&RA Rigging Job of the Year (JOY) awards, presented at their annual conference in California. The awards recognize worldwide excellence in the crane, rigging and specialized transportation industry.
Here’s how the projects unfolded:
Scrubber Support
Barnhart’s Philadelphia branch received the call from the plant to provide emergency structural support for its two 120’ tall, 600,00-pound scrubber units. The outer walls of vacuum chamber in the scrubber had significantly degraded, which put the unit at risk of a total collapse.
The situation required immediate action. In addition to safety concerns, the plant was losing about $500,000 a week in lost power generation. Barnhart’s engineers had to develop a high-capacity shoring system to place in a tight and congested footprint in a short window of time.
The solution was the erection two identical modular lift tower frames (MLTs) to extend up and over the scrubber. Pull-up gantries were installed on the bridge assembly of the towers to provide tension to the system. Custom length high-capacity wire ropes were designed and fabricated to support the height of the scrubber units. The system was able to support the full weight of the scrubbers and eliminate the possibility of a collapse.
With the MLTs erected, the plant safely began repairs by fitting and welding cladding sheets. The MLT system also allowed the place to operate the units while completely repairs, greatly reducing downtime.
The solution resulted in a Rigging Job of the Year award over $2 million.
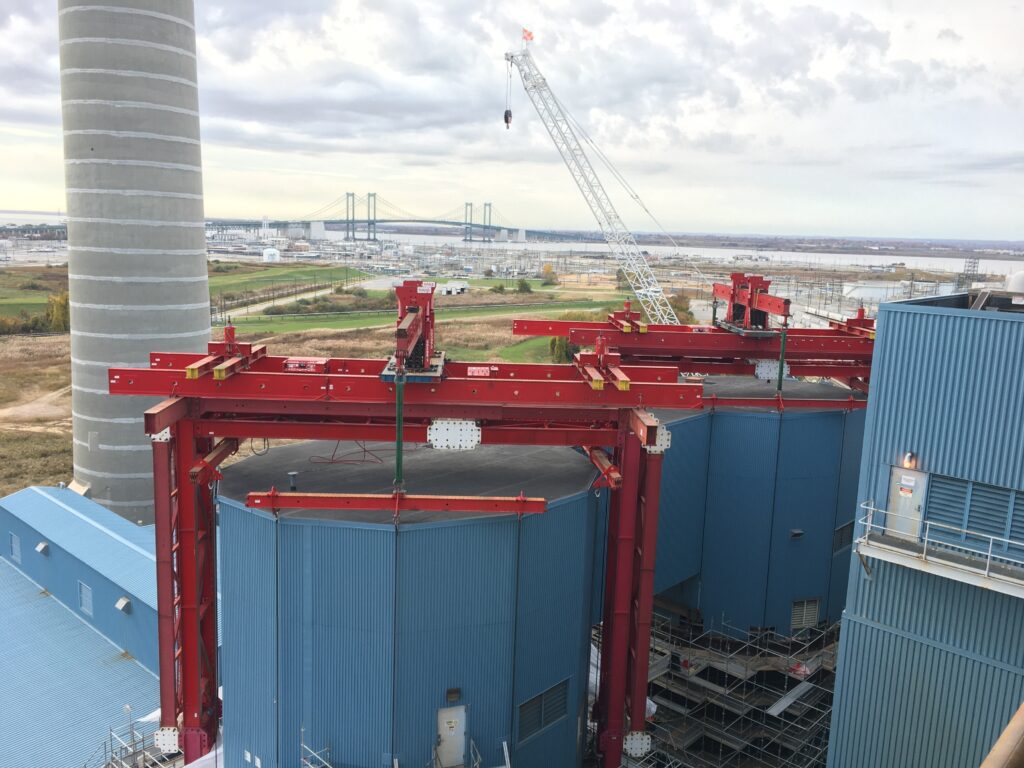
Call in The Claw
When Barnhart’s Mobile, Alabama branch was hired to remove and replace 12 reactor legs at the Florida plant, the clock was ticking. The legs were critical pieces of equipment, vital to plant operation.
The reactor legs were in a tight location with no easy way to lift them out without removing multiple obstructions. Having never been replaced before in 50 years of operation, there was no known method of removal. Each leg weighed 12,000 pounds and was 50’ long and 16” in diameter.
The solution was to utilize a moveable counterweight cantilever system (MOCCS), which reached under the structure and connected to the reactor leg with a welded lug pinned off to our system. A custom-designed manipulator arm known as “The Claw,” wrapped around the leg and was bolted securely.
Two chain falls and straps were used to hold the vertical load. Two hydraulic cylinders allowed for rotation of the reactor leg from vertical to horizontal. The leg could then clear any obstructions as it was lifted upward and out.
This alternative method reduced the schedule from 14 days to 7 days, which was extremely valuable to the site’s project management team.
The job was awarded a Rigging JOY $150K – $750K. See The Claw in action below.
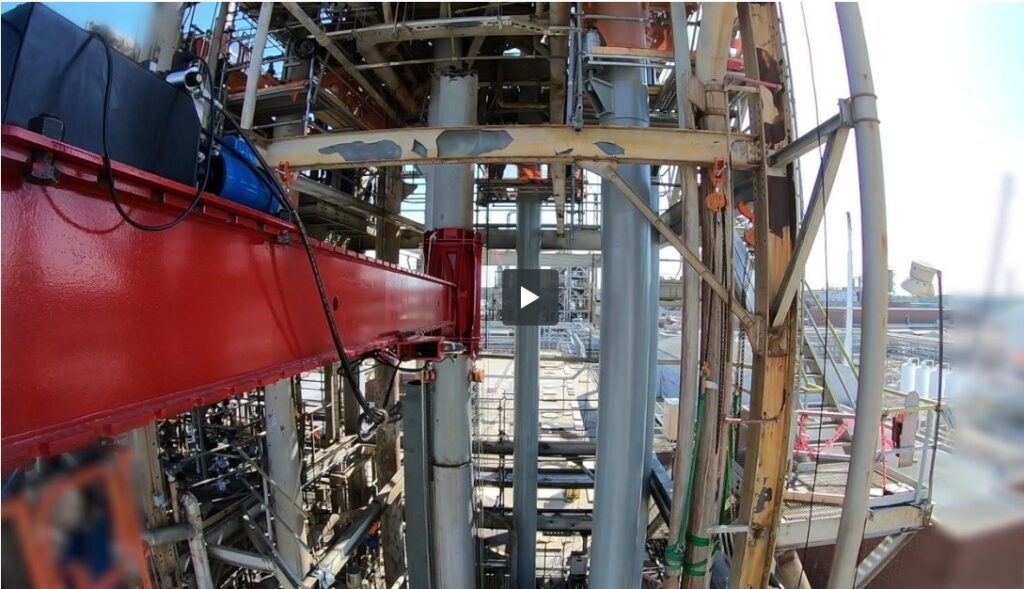